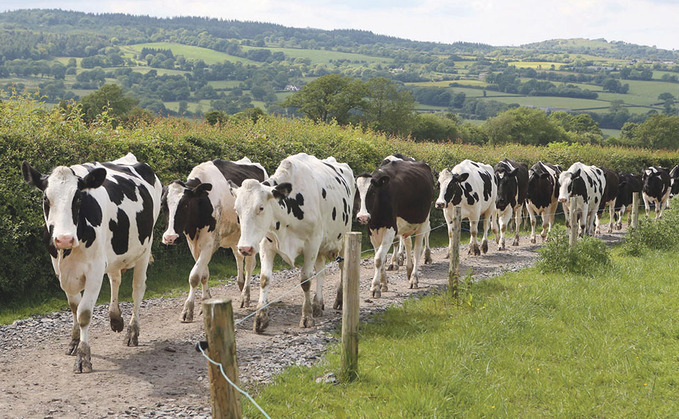
A good track can extend the grazing period and improve access to fields, as well as bringing benefits to cow health, so what should farmers consider when putting one in? Ruth Wills reports.
Designed and installed correctly, cow tracks can bring benefits to grazing, cow flow and welfare, but get it wrong and it could be a costly mistake.
David Ball, of the environment and buildings team at AHDB, says the first consideration is to ensure enough space for cows.
The track width should be at least four metres for up to 200 cows, with an extra metre for every additional 100 cows.
He says: "Cows walk with their head down and think about where they place their feet. They need space to do this, therefore a good track will reduce lameness."
He adds that cows like to walk in order, which is dictated by the more dominant leaders, and this may not be the same as the milking order.
"There needs to be space for them to reorder themselves before they enter the collecting yard. There are those which prefer to walk ahead but not be milked first."
Mr Ball says next it is important to think about the positioning of the track.
He says: "The positioning may be obvious, but avoid hollows, shaded areas and sharp turns, as these all increase wear and tear and make drainage difficult.
"If necessary, follow the contour round the hill. Cows would rather walk further than up and down hills."
Unless the track is on a slope, there needs to be a camber to drain the water off, says Mr Ball.
"If there is loose material, such as stone or woodchip, the maximum slope should be 12 per cent to avoid surface material washing off. Install cross drains or speed bumps to capture run-off."
With hard material, such as sleepers, which allow drainage between them, the slope could be greater. Mr Ball advises keeping vehicles off tracks. He says: "They are made for cows not for tractors."
Stone
Stone is a great material, says Mr Ball, but there are different grades and something which is suitable for the track foundation might not be suitable for the surface.
He says: "Start with larger stone at the base, which is good for drainage, before building up to a fine material on the surface. Each layer needs to be well compacted and the top surface needs to be free from sharp objects."
A geotextile membrane can be used to create a barrier between the soil and the stone, preventing mingling of materials over time.
Mr Ball says: "A vibrating roller should be used to compact each layer. Ensure there is a camber of 20cm in the middle of track."
One benefit of using stone is that the material is often readily available and relatively cheap, but it requires maintenance and is essential to get the drainage correct to prevent water damage, says Mr Ball.
And check waste regulations for materials: "For crushed bricks and blocks you might need a U1 waste exemption from the Environment Agency."
Case study: Trink Dairy, Cornwall
Chris Knowles, a third-generation farmer at Trink Dairy, St Ives, Cornwall, uses artifical grass on his cow tracks.
Previously the tracks were made of a granite mixture, but were prone to forming gullies in heavy rain and, after 20 years, it was starting to erode.
Following a visit to Bicton College, which was using artificial grass on its cow tracks, Mr Knowles was sold on the idea.
He says: "My local hockey club in Penzance received a grant to replace its pitch and asked if I wanted it."
He received 200 rolls of 50ft by 6ft artificial grass.
Mr Knowles says: "I am very pleased with it. For foot health it is a miracle. It is so gentle, it seals off the track and when it rains the artificial grass washes clean."
Over the past five years, Mr Knowles has covered 70 per cent of his tracks with artificial grass.
"There are still some bits which are difficult when wet, so I would not put it on a very steep slope."
Although the first delivery he had cost about £20/roll, later purchases rose to £30/roll.
He says: "I have heard people pay up to £70/roll, but even at that I think you could justify it if you used it in strategic places."
To make the track wide enough, Mr Knowles overlapped it in places, and has learned its limitations over the years.
"In mid-autumn when it is wet, cows drag mud onto it and make it slippery. I have on the odd occasion put some sand down, then the heavy rain comes and washes it clean again."
With an extensive grazing system across 110 hectares (272 acres) and with 330 milking cows, Mr Knowles plans to cover more of the tracks in the future.
He says: "As the other tracks start to erode we will cover more, but you cannot cover up anything which is protruding; you have to have a reasonable structure underneath.
"Cows are very happy. With the extensive grazing system, autumn can be difficult on their feet, but it has helped a huge amount."
Farm facts
- 263 hectares (650 acres), of which 52ha (128 acres) is moorland; all owned
- Two full-time members of staff plus Mr Knowles
- 75 per cent Friesian and 25 per cent Jersey cows
- Averages 3,800 litres/cow/year
- Milk sold through Arla Co-operative, local farm shops and milk vending machine
- Spring-calving
- Extensive grazing with a small amount of concentrates
- Once-a-day milking in a 24/48 swingover Milfoss parlour
- 20 per cent replacement rate, aiming for 17 per cent
Woodchip
Woodchip has good drainage and is a consistent size throughout, but it has become more expensive.
Mr Ball says: "There needs to be a geotextile membrane and a good depth of material which helps make it softer for walking on. Depending on soil type, you might need up to 20cm of woodchip."
He adds that depending on the source, it is a good idea to screen the woodchip for foreign objects such as screws.
In terms of maintenance, some farmers have designed mechanical rakes to rake the surface material back to the centre.
Mr Ball says: "It might need topping up periodically due to use and weather. It has the potential to get stuck in cows' feet, so choice of material is important."
Sleepers
Sleepers are quite popular because they are durable, but they are not the cheapest option, says Mr Ball.
"They are perhaps preferred because they are transportable, flexible over where they can be placed and they will go on for years."
Sleepers need to be laid directly on the soil surface, not dug into the ground, as that will help water drain.
Mr Ball says: "Sleepers might be more suitable on increased slopes. However, because it is a hard surface, foreign objects on the track can cause problems with feet."
Artificial grass
Artificial grass is often used as a top cover on existing tracks to improve the walking surface, reduce weathering and wear and tear, says Mr Ball.
He says: "While this acts as a protective layer to improve the surface and longevity, artificial grass is not suitable for use on its own."
It will also reduce drainage properties and can be slippery when wet. Availability and price varies across the country.
astro pic
Case study: Ditchetts Farm, Devon
Richard Tucker at Ditchett's Farm, Tiverton, Devon, is using stone and concrete on his cow tracks and has seen a vast improvement in herd lameness.
On an extensive grazing system, cow tracks are important, he says. "A lot of the previous tracks were made from stone dug out from the farm and clay, which worked well for quite a few years."
But as herd numbers crept up, problems started to arise.
Mr Tucker says: "We had a wet summer in 2017 and really suffered with white line issues; about 15 per cent of the herd was lame."
He thinks this was caused by cows slipping on tracks, which were steep in places, so he decided it was time for a new approach.
He says: "I saw a few different tracks and, although I liked the look of artificial grass, our farm is too steep. I decided to go with a mixture of concrete and stone."
On the high-use tracks, such as the ones close to the yard, he used grooved concrete, while for the rest he imported clean stone, graded down over 6in into a dust on the surface.
"We then rolled it with a vibrating roller, added scalpings on top, and rolled it again," he says.
Mr Tucker has redone 80 per cent of his tracks and hopes to finish the rest this year. "The whole thing came to £3.50/metre, including labour."
And it is been money well spent.
He says: "The difference was amazing, it took half the time to bring cows in from the furthest field and we have only had one new case of white line disease in the last year, so it has saved us a lot of time."
Farm facts
- 124 hectares (306 acres), with 64ha (158 acres) grazing; all rented
- Farming in partnership with parents Brenda and Nigel
- Spring block calving
- 240 cows plus 120 followers
- 75 per cent Friesian and 25 per cent Jersey
- Richard, Brenda and Nigel all full-time with one relief worker
- Selling milk to Arla Co-operative